In our collective search for bright spots during this global crisis, the commitment of the scientific community stands out. We’re proud to highlight their work.
We recently shared details of our involvement with the UBC Rocket Engineering Design Team, their design program, and why they chose Haskel as their gas booster supplier. In a check-in on their most recent accomplishments, the team was very excited about the successful hot fire testing they have completed. This is a major milestone for any rocket team, but especially for UBC since they were the first Canadian student team to do so.
Though the team is currently working remotely due to COVID-19 closures, we spoke with the team’s propulsion testing lead, Griffin Peirce, to learn more about the hot fire accomplishments and the goals they are pursuing even through remote work.
How did you get involved with the UBC Rocket program in the first place?
Most members join through our annual recruitment as it is available to anyone who attends the University. I came into the program differently than most who join; the captains of the team bumped into me in passing and asked if I could help rebuild a lathe for them. During the couple of months I was helping the team, I grew close to a lot of amazing people in the program. Over time, my responsibilities continued to grow, and I began working in the propulsion testing group. This eventually led me to my current position of heading up our hot fire operations where I oversee the development of equipment, such as testing rigs and software, to evaluate the team’s prototypes. It is an honor to be a part of UBC Rocket and to work with brilliant colleagues from all different backgrounds and majors of study. Our team has done some amazing things in the short time that our program has existed. Since forming three years ago, we have become a leader among universities that have 10+ years of experience.
Your team has a goal of eventually sending a rocket into space (300,000 feet). What are the team’s immediate goals for 2020 that will prepare you for the ultimate launch?
To send our rocket into space, our propulsion team is striving to develop a reliable propulsion system and have a large portion of the rocket built. Designing the propulsion system takes a lot of time and even a small oversight can lead to our hardware being destroyed during a test, so planning plays a crucial role while running tests. These goals are an interesting challenge because while there is a lot of literature on the function of rocket engines, the constraints of equipment, budget, and time mean that the real challenge is designing an engine that is within our means to manufacture. This means that we focus heavily on evaluating different manufacturing techniques to build the simplest engine design that meets our performance specifications. Testing early, make changes quickly, and adjusting plans are all key to minimizing risks in the project.
Can you tell us more about the hot fire testing successes and what it means for future launches?
For each model we build and test, we characterize the performance based on the engine’s pressure, mass flow rates, thrust, and temperature, to name a few of the key parameters. There are several precursor tests we run on hardware before it reaches the hot fire stage, so when we conduct a hot fire, the hardware we are evaluating is the culmination of significant manufacturing and testing effort. The hot fire is an important test on the propulsion system that ensures each part of the engine is working properly.
The type of performance we look for is similar to how one might grade a car engine. For example, we want an engine that uses our fuel and oxidizer efficiently so that we are not carrying extra propellants and adding to the rocket’s mass, we want an engine the provides sufficient thrust to safely launch our rocket, and we want to ensure that it will not overheat and fail while it operates. These are just a few of the main considerations and naturally, these performance characteristics have trade-offs that influence the design, and as I have mentioned manufacturing a system to achieve this is difficult. The engines we are developing are built to be simple, robust, and reliable, to loop back on the car analogy, you can think of our engine as being on the tractor end of the spectrum whereas the engines you see being used for commercial space flight are like sports cars by comparison.
Our test stand is essentially a mobile structure about the size of an SUV that simulates the propellant feed system on a rocket. It provides a reliable interface onto which we can attach and test an engine. We have upwards of 50 different sensors to monitor system pressures, temperatures, and thrust which help us confirm that the engine is operating as predicted.
We are currently in the early phases of single-engine testing. When planning for a day of testing, a week is spent making sure all systems are prepared for test day. A full day’s worth of operation is required to conduct our hot fire tests with the test only lasting a couple of seconds. Once the test is complete, it takes the team a little less than an hour to reset to run another test. As we continue testing and getting more efficient, we can reduce the cycle time on engine testing and also move to longer tests as we become more confident in the hardware.
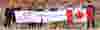