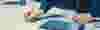
4 Steps for Planning Your High-Pressure Gas & Liquid System Purchase
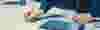
Designing a system for delivering highly pressurized gas and liquids requires engineers to successfully meet the challenge of achieving necessary flow input while mitigating potentially dangerous flow failure situations. The unique needs of the application the system is being used in must be carefully considered prior to the purchase of system equipment.
Ensuring our customers are working in the safest and most efficient high-pressure environment possible is a top priority for our Haskel team. The following four steps will help when planning high-pressure flow systems and purchasing the necessary components:
1. Create a robust design which addresses your unique high-pressure applications and specifications.
In order to plan an optimal high-pressure system, it is critical to consider specifications related to each unique application and needs for safety, continuity of flow, type of inputs being used, any environmental or systemic constraints, and budgetary considerations. It is often beneficial to begin with a comprehensive high-pressure system design and then make modifications based on any necessary environmental, organizational, or budgetary compromises.
Another key element of the planning process is determining whether a brand new high-pressure flow system is necessary or if an existing system can be retrofitted for improved functionality and efficiency. Examining your existing equipment can significantly save costs if it’s possible to reconfigured it to meet new standards or applications.
Regardless of whether planning involves an existing high-pressure fluid system or the design of a new one, most modifications to the initial designs are driven by cost, organizational needs, component performance, ecological factors and equipment-specific considerations. Some examples include:
- The need to incorporate fluid power or gas boosting components into a design.
- High-purity gas or liquid cleaning to reduce the risk of contamination.
- Implementation of multi-staging flow capabilities within an application.
- The measurement of flow rates and the pressure standards specific to an industry or type of application.
The decision to utilize standardized components or to seek customized solutions is also part of the initial planning process for high-pressure gas and liquid systems.
2. Evaluate the performance and reliability of potential components.
Once a high-pressure system for gases or liquids has been designed, the next step is to assemble the necessary components and make a plan to implement any necessary modifications to existing infrastructure. It is important to use standardized criteria when comparing components for a high-pressure flow system. Some elements of a high-pressure system to consider:
- The degree of head-loss for valves which can lead to higher energy costs from increased pressure loss.
- Proper selection of valve closures to prevent non-slam characteristics
- Matching of the valve style with fluid type for compatibility with the desired function.
- Selection of compatible seals to determine whether drop tight, gas tight, or bubble tight seal is the optimal choice.
- Flow characteristics on all check valves to make sure sudden surges or shutdowns do not occur.
- The need for leakage compensation features which can create an initial high flow rate to clear flammable gasses then maintain a minimum pressure threshold.
3. Develop a budget for potential system components.
Another element which must be taken into consideration when planning a high-pressure flow system is, of course, the organizational budget. Both the components you select and the vendor you choose to supply them will factor into the budget you create for your high-pressure flow system. Both the initial costs and maintenance costs over the long-term should be factored into your final design. Poorly fitting components or ones not made to meet the specifications necessary to your application are likely to increase life cycle maintenance costs over time.
Generally, the more complex your high-pressure flow system requirements are, the higher cost your components will be due to their added functionality. Beyond the initial price point for valves, pumps, cylinders and other components, consider any additional installation costs as well as any value-added services such as consultation or maintenance plans. Working with trusted suppliers in the industry will help you ensure you’re getting the best value and the right components for your application. This could be a good opportunity to evaluate your supply chain and find the best partners for your project.
4. Take advantage of external expertise.
Designing a high-pressure flow system for gases or liquids can be a complex and time-consuming process. Given the variance in application requirements, safety concerns, budgetary constraints and the multitude of available components, consulting with experienced specialists will usually yield the best results. Doing so will also allow your organization to utilize an objective third-party view and receive valuable feedback on potential risks, as well as have access to best practices in high-pressure flow system design.
If you are planning to design a high-pressure gas or liquid flow system, the four steps above can help you get started.